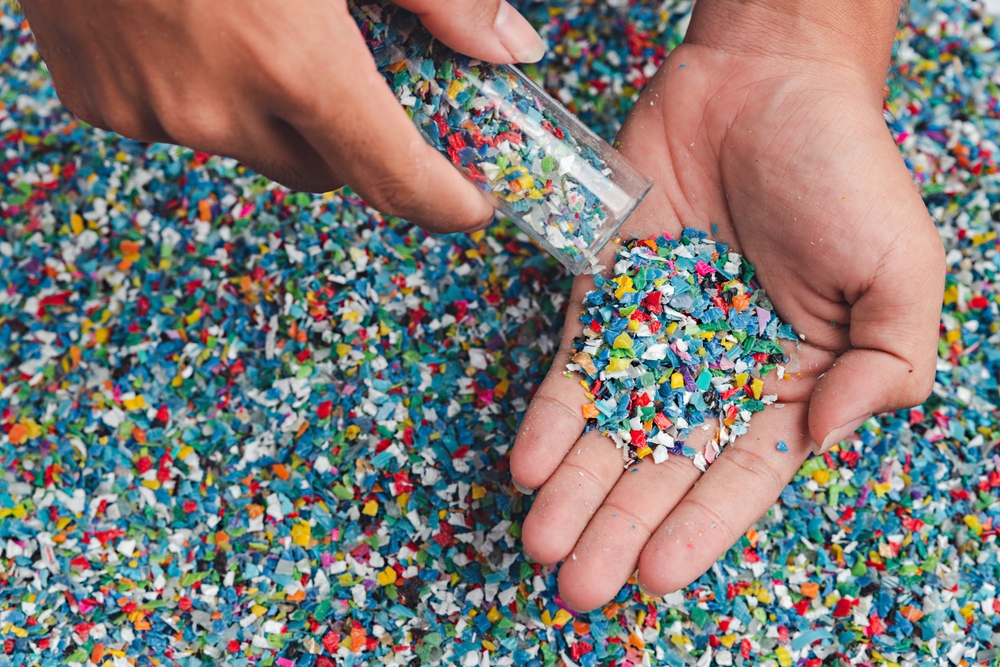
Proposing the ACTPAC Framework to Enhance Industrial Recycling and Upcycling of Plastic Waste
The industrial sector plays a central role in reshaping the value chain of plastic waste and serves as a key enabler of pioneering technologies and manufacturing approaches. As a non-governmental organization, the Alliance to End Plastic Waste, which includes Chevron, Dow, ExxonMobil, LyondellBasell, Procter & Gamble, Shell, Total, Veolia focuses its resources on developing waste collection infrastructure advancing recycling technologies and product design, educating consumers about waste management, and cleaning up plastic in the environment [1].
In the current industrial efforts to create new value out of plastic waste, two main approaches are generally distinguished: recycling and upcycling. There are two fundamental methods for reusing plastic: (1) mechanical recycling, and (2) chemical recycling. Mechanical recycling involves processing waste materials into secondary raw materials without altering their basic structure. In chemical recycling, a plastic polymer is broken down into its constituent monomer. The monomers are used as raw materials for manufacturing a new polymer. Mechanical recycling is a more maturer technology, with some processes already implemented at large pilot scale (TRL 8–9) or in full production. On the other hand, many chemical recycling methods, including pyrolysis or (chemical/enzymatic) depolymerization, remain at the development or small pilot scale stage (TRL 7-8). To date, chemical depolymerization efforts have primarily focused on the depolymerization of PET, poly(ethylene terephthalate), which contains a hydrolysable ester bond [2].
The following table presents a selection of
representative industrial efforts aimed at the valorisation of plastic waste.
Leading companies | Project title | Main actions / Technology | Products / outcomes | Information source |
---|---|---|---|---|
BASF | ChemCycling | Pyrolysis is used to transform plastic waste (either mixed plastic waste or end-of-life tires) into a secondary raw material (pyrolysis oil). This oil is fed into the BASF’s production network (Verbund) at the beginning of the value chain, thereby saving fossil resources. | The resulting products have the exact same properties as those manufactured from fossil feedstock, and can be further processed in the same way as conventionally manufactured products. | Link |
DOW | Teamed with Dow X Circulus, Freepoint, Mura Technology, Valoregen, Plastogaz | Plastics are separated; Plastics are shredded; Reusing plastic; Converting plastic waste | Used the recycled plastics as packaging materials in food and medical applications | Link |
Eli Lilly, Sanofi, Merck, Novo Nordisk | ReMed™: Recycling used device | The project works on expanding the programme globally to reach more people, and with every injection pen collected and recycled through the support of our patients and partners, we’re one step closer to our ambition of zero environmental impact. | Reused for manufacturing medical device | Link |
Merck | SHIFT: CREATING CIRCULAR RECYCLING SOLUTIONS | Through engagement and collaboration with their customers, Merck will be able to develop circular recycling solutions to reduce the amount of plastic in the value chain and offer cost-effective re-processing of the plastic waste back into products and packaging within their supply chain. | Merck has made assessment guide and tools that can be used by an individual or an entire lab to measure the amount and types of plastics and how they are being disposed in the lab. The data collected from these assessments provides a plastic benchmark to measure and track changes within your lab. | Link |
GR3N | C-PET | The project involves two key steps: accelerated depolymerization and highly effective downstream purification. We entered cPET project by having reached TRL6–7 thanks to previous EU-funded projects (i.e., SYMBIOPTIMA and DEMETO) on both microwave-accelerated depolymerization and purification of PET. | With cPET, the TRL 8 for both lines of development, with the reactive unit prototype inside GR3N’s demonstration plant will be achieved, playing the role of last “testing equipment” before going into series production. | Link |
An overview of the listed industrial initiatives reveals several key observations
1) The initiators of the leading companies are from different industrial sectors from energy producer to medical/pharma supplier, indicating the seriousness of plastic waste threats to our environments and sustainability concerns.
2) Most industrial actions are focused on the pyrolysis of plastic waste into fuels and chemicals, a process that typically has relatively low selectivity and yields a broad spectrum of products.
3) New value chains from plastic waste are still being developed primarily through chemical methods, often involving only a limited range of plastic types and a few processing steps, mainly by reversing polymerization into virgin monomers.
In contrast, the ACTPAC project defines its mission as achieving breakthrough technologies, processing methods and production lines that enable the generation of a wide range of new fine chemicals (such as alkanes), monomers (diols and diacids) and biodegradable polymers. These polymers may be either homogeneous or heterogeneous, with varied chain lengths. The project targets hard C-C backboned polyethylene. The approach integrates both chemical and biological transformation steps. The technology developed within the ACTPAC Project characterized by flexibility, controllability, selectivity and adoptability for small and medium-sized enterprises (SMEs), making them responsive to market demands. The emerging ACTPAC technology clusters aim to establish a new horizon for reshaping the plastic waste value chain. (https://cordis.europa.eu/project/id/101135289)
Author: Zheng Guo, Aarhus University
References
[1] 18 March 2024, ‘Industrial demonstration plant to depolymerize and rebuild PET opens its doors’, Packaging Europe, Mar. 18, 2024. Available: https://packagingeurope.com/news/industrial-demonstration-plant-to-depolymerize-and-rebuild-pet-opens-its-doors/11101.article. [Accessed: Apr. 14, 2025]
[2] Alliance To End Plastic Waste, ‘Alliance To End Plastic Waste’. Available: https://www.endplasticwaste.org/. [Accessed: Apr. 14, 2025]
Keywords
Plastic recycling, waste plastics, recycling, value chain, pol